Finding optimum architectural design for an automated warehouse
The context and the problem to be solved
The primary challenge faced by our customer design teams stemmed from the difficulty in assessing how fluctuating operating conditions (such as managing activity spikes during Black Friday or Christmas, and accounting for traffic congestion causing irregular truck arrivals at the warehouse) impacted the overall performance of the automated warehouse. This created a need for a flexible tool that could assist the design teams by providing simulation support. The goal was to enable informed, high-level architectural decisions while avoiding the time and expense of conducting detailed analyses on non-viable warehouse configurations under varying conditions.
➤ In essence, the main customer requirement was to determine optimal design solutions for an automated warehouse under changing scenarios, while considering all commercial and industrial constraints and risks.
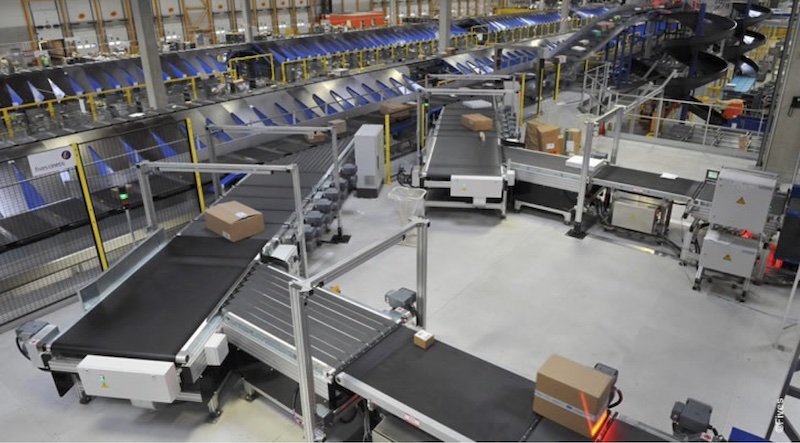
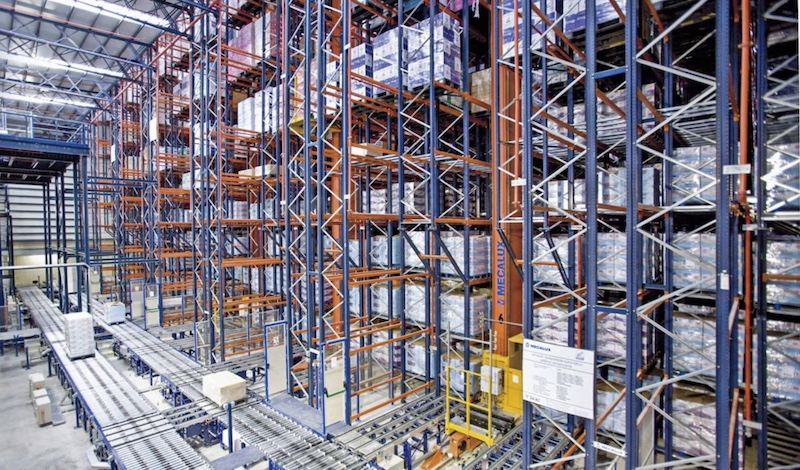
Our solution
In response to the design and operational challenges posed by our customer, we developed a comprehensive digital model of a standard automated warehouse. This model encompassed an exchange infrastructure, an automated storage area, and multiple robots responsible for transferring packages between the external site and the storage zone. Subsequently, we integrated this digital twin into the warehouse design process, enabling the design team to simulate and assess various design options tailored to each client’s needs in order to determine optimal solutions. Furthermore, this tool can also serve as an operational aid by alerting operators to any irregularities in the automated warehouse’s performance during its functions.
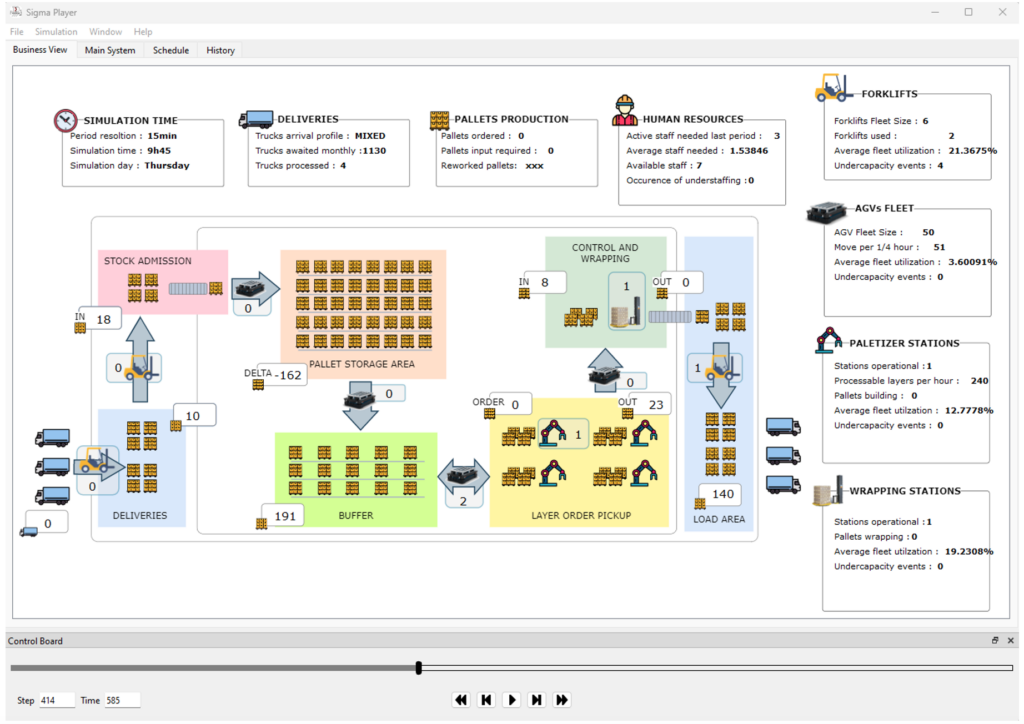
Customer benefits
➤ Our client initially highlighted the primary advantage of our approach as establishing a unified and comprehensive quantitative overview of an automated warehouse, which was previously absent.
➤ The ultimate advantage of our approach was the ability to pinpoint the most suitable design decisions for an automated warehouse by considering all relevant commercial and industrial limitations and risks that it encounters.
Our detailed technical approach
What was the system of interest?
In the case being considered, the system of interest was a new generation automated warehouse that enables logistic operators to supply points of sale in densely populated urban areas. Such automated warehouses need to be compact and fast to handle high demand within a small physical footprint. Traditionally, they produce heterogeneous pallets that are constructed without specific ordering from individual boxes, thanks to a fleet of robots known as automated guided vehicles (AGVs). In this scenario, our customer wanted to introduce a new mode of operation with a palletizer robot system capable of processing entire layers of a pallet at once. This advancement allows for a significant reduction in the operating time of an automated warehouse.
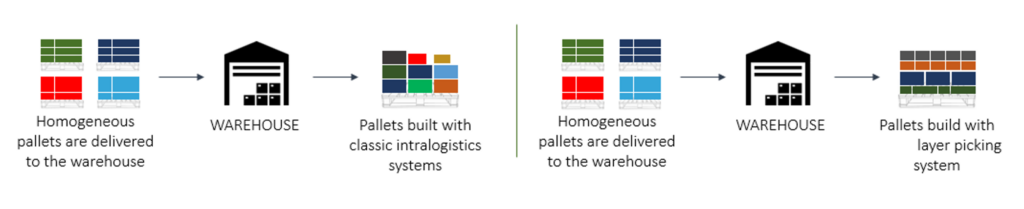
The automated warehouse consists of two pallet delivery and load buffers for handling pallets at the start and end of production. It also has two storage input and exit buffers where warehouse operators manually manage pallets with forklifts. The pallet storage area stores incoming pallets until they are needed to create output pallets. In the palletizer area, a robot arranges output pallet layers using a local buffer. Subsequently, all output pallets pass through a wrapping station for plastic wrapping.
Transportation of pallets between the storage input buffer and exit buffer is overseen by automated guided vehicles (AGVs), which are shared resources. Human operators and forklifts in this setup are considered as other shared resources within the automated warehouse environment.
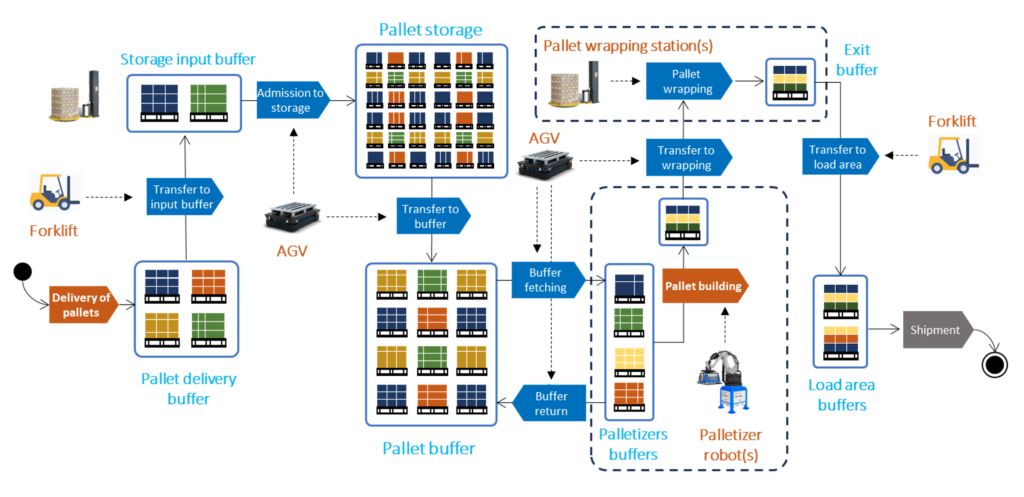
Analyzing the behavior of the system of interest using the types of activities and of flows introduced in the previous industrial customer cases, one can then obtain the abstract model of the considered automated warehouse which is presented in the figure below. All industrial activities presented in this figure are managed in parallel and the corresponding activity flow is triggered by the input pallet flow.
One can especially observe that the system of interest can again be described with the same generic types of transform, store and transport activities and of physical flows that were introduced in the previous customer case analyses, as illustrated in the figure below.
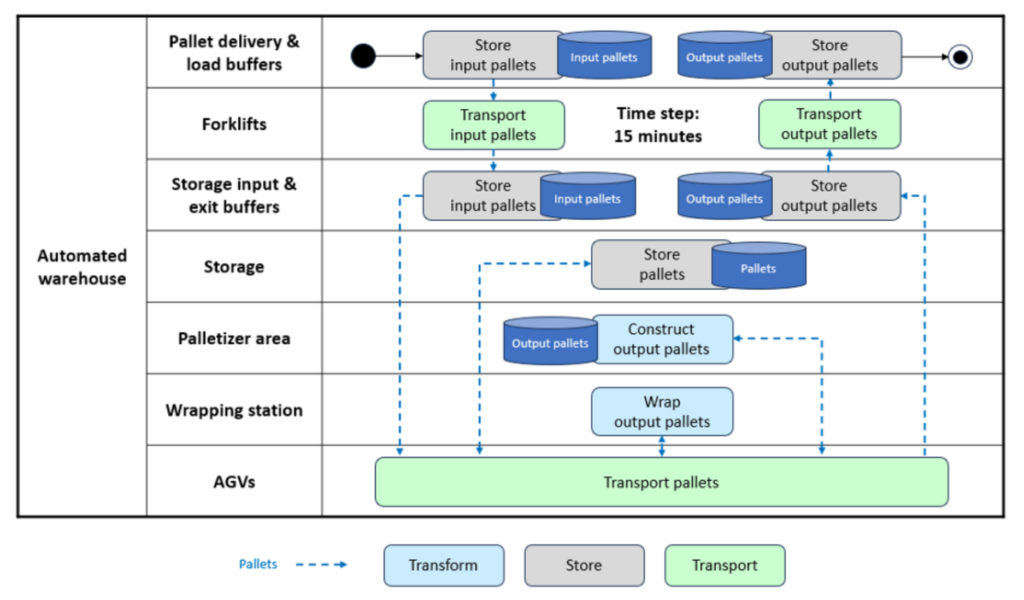
What was the proposed solution?
To answer the design challenge of our customer, we constructed a systemic digital twin based on a parametric model of the considered new generation automated warehouse. The parameters of our systemic digital twin are here the weekly input pallets flow, the output pallet delivery profile, the quantity of warehouse human operators and the amounts of automated devices (forklifts, AGVs, palletizers, wrapping stations). The systemic digital twin simulates then a typical operating day of the automated warehouse.
Our systemic digital twin can be first used in a step-by-step simulation mode (cf. Figure below for an illustration) in order to understand & explain how the model works and to simulate various industrial scenarios with objective to find the best one. This step-by-step mode is typically used for an initial study of the automated warehouse, with focus on the identification of the conditions that are leading to bottlenecks.
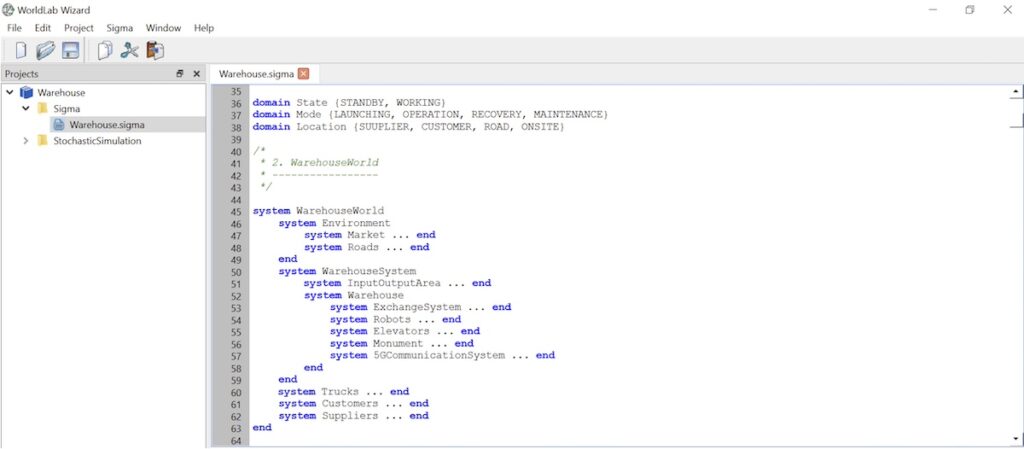
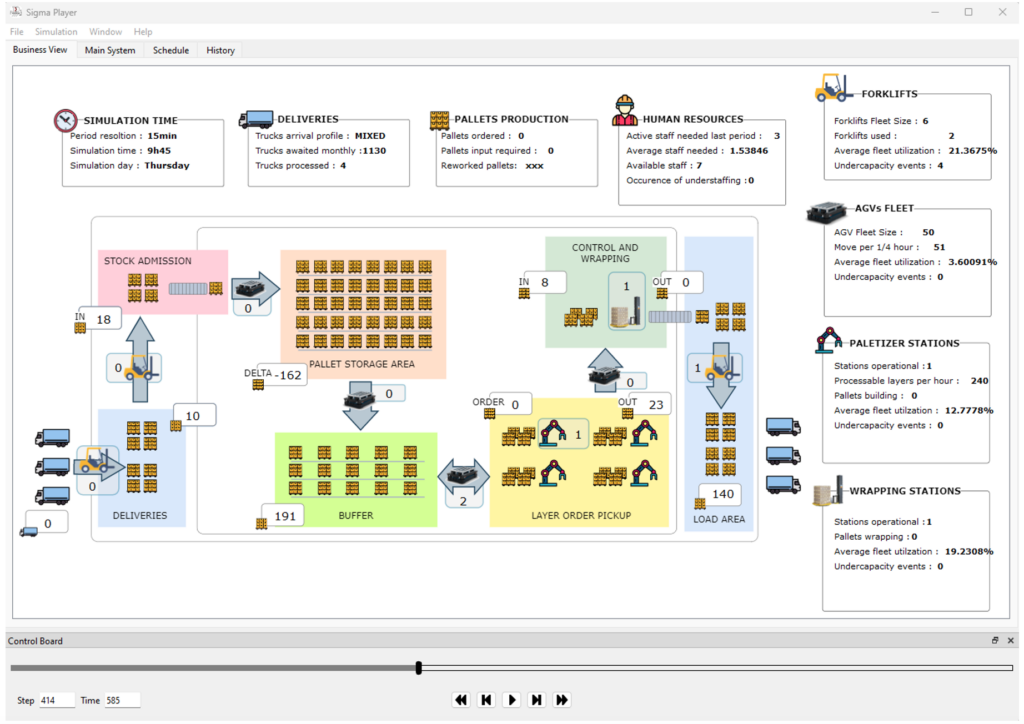
The systemic digital twin can be also used to manage stochastic simulations where we are simulating several thousands of operating days in order to understand the statistic dispersion of the key performance business indicators that the systemic digital twin has to compute to meet the expectations of the business users as aligned with the targeted customer needs.
Figure below shows an example of results of such stochastic simulations in a situation of peak of orders (the output pallets to produce per day are here doubled with respect to the usual nominal situation, the other parameters of the automated warehouse being unchanged). One can then see that a backlog of unprocessed output pallets is statistically forming and that AGVs and palletizers are over busy during an average such peak day. Based on these observations, one can then again use the systemic digital twin to test alternative dimensioning of the automated warehouse in order to face and correct these issues.
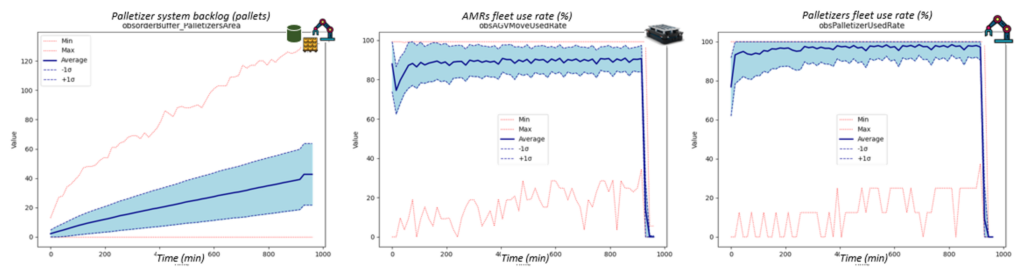