WorldLab™ for industrial processes
Resilience of industrial processes
➤ CHALLENGES
Industrial resilience is a critical concern for businesses operating in sectors such as manufacturing, energy, aeronautics, and automotive. As global markets become more interconnected and regulatory environments increasingly stringent, large enterprises face numerous challenges in maintaining operational stability. One key issue is supply chain disruption, which can be triggered by events such as natural disasters, geopolitical tensions, or sudden shifts in demand. These disruptions often lead to delays in production, higher costs, and in some cases, a complete halt in operations, threatening both profitability and market share.
Additionally, regulatory compliance is a growing burden for industries. Constantly evolving environmental, safety, and labor laws require businesses to adapt quickly, often involving significant changes in processes or technologies. Non-compliance can result in fines, legal actions, or reputational damage, all of which erode a company’s resilience.
Another common issue is the complexity of scaling operations. When businesses expand, adding new production lines or entering new markets, they often encounter bottlenecks. These can stem from outdated processes, inadequate infrastructure, or poorly integrated systems, all of which reduce efficiency and flexibility. Without the ability to scale smoothly, companies struggle to meet growing demand, which in turn impacts customer satisfaction and long-term growth prospects.
➤ SOLUTIONS
Addressing these challenges requires a systemic approach. Industrial resilience is not achieved through isolated fixes but through the careful coordination of processes, technology, and human resources. Companies need to adopt advanced planning tools and strategies, such as digital twins or simulation models, to stress-test their operations under various scenarios. These simulations allow businesses to anticipate disruptions and identify weak points before they escalate into major issues. By doing so, they can make informed decisions on how to optimize supply chains, comply with regulations, and scale efficiently.
Ultimately, building resilience is about creating a business model that can withstand shocks, adapt to changing environments, and continue to grow sustainably. Large enterprises must invest in the right tools, talent, and processes to ensure that their operations remain agile and capable of responding to both immediate threats and long-term challenges.
➤ WorldLab™ for industrial processes
Whatever the systemic level of your concern: production floor, manufacturing plant, multi-site manufacturing systems or large-scale industrial network, etc., WorldLab™ can help you finding optimum configurations for existing / new infrastructures or industrial transformation projects and facilitate your day-to-day/month-to-month decision-making for the industrial systems that you operate.
Case studies
Finding optimum architectural design
for an automated warehouse
The challenge
Our client sells highly automated warehouses. However, the operations of a warehouse depend greatly on the season and of the availability of human & technical resources which may vary over time. In order to make the best system-level design decisions, it was necessary to obtain, for a given warehouse configuration and in a given operating scenario, key quantitative insights on the logistic macro-performances of the automated warehouse in order to be able to compare various possible competing industrial architectures and find the best solution to efficiently prepare more in-depth engineering analyses using dedicated tools.
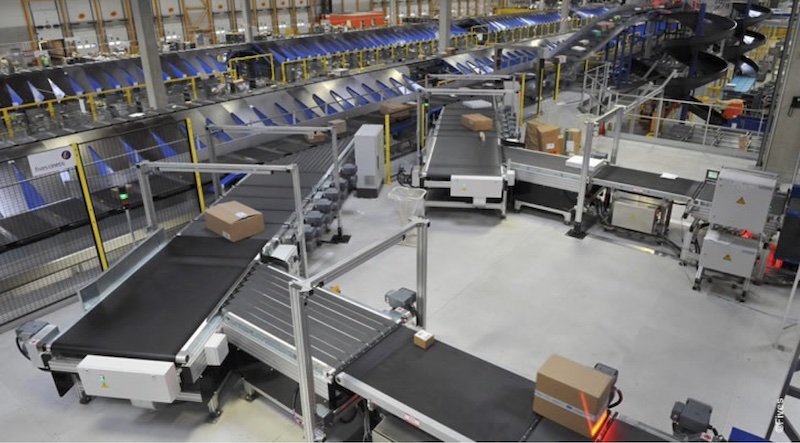
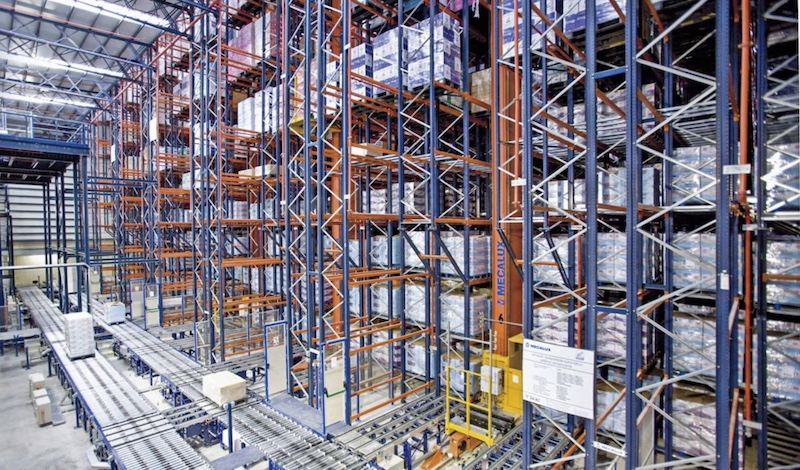
Our approach
To answer our customer design & operation challenge, we constructed a systemic digital twin of a generic automated warehouse that included an exchange infrastructure, an automated storing zone and a number of robots that are moving back & forth packs from outside the warehouse to the storage zone. We equipped then the design process of such a warehouse with it, which allowed the warehouse design team to simulate & evaluate a number of design variants for each customer and to identify the best ones. The same tool can then also be used in operation mode to alert the operators of an abnormal behavior of the automated warehouse during operations.
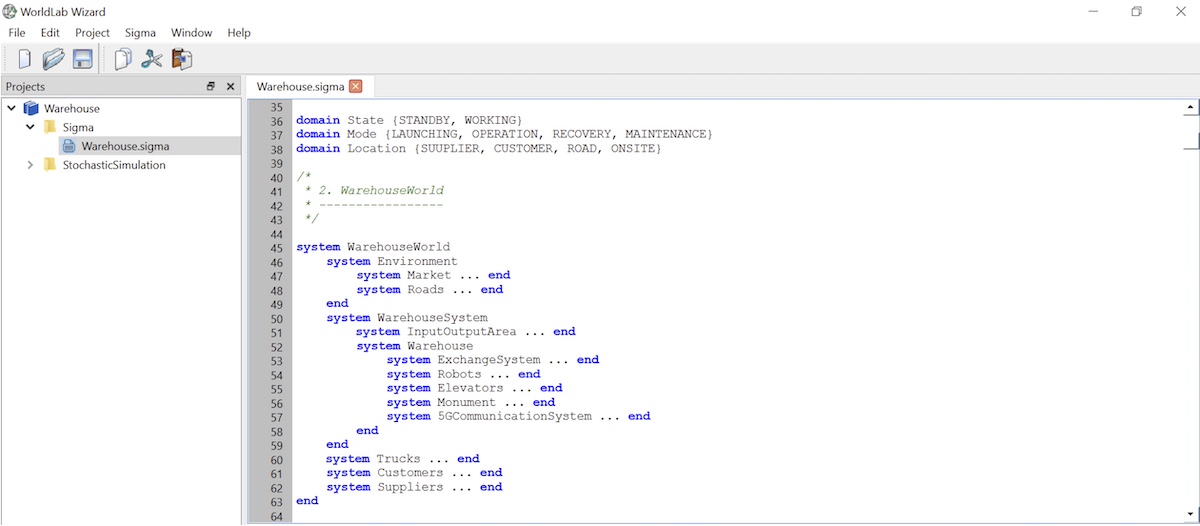
The outcomes
FEATURES
Service features that were deployed:
– Structural & behavioral modeling of an automated warehouse
– Analysis of operational data of an automated warehouse environment
Product features that were used:
– Implementation of a systemic model in Σ™
– Connection with external & internal data sources
– Step-by-step and stochastic simulation
– Scenario simulation and evaluation
ADVANTAGES
Traffic trends were modeled & simulated in order to capture the evolution among time of distribution traffics which are the core outputs that trigger the inputs of an automated warehouse.
All business & industrial hazards & perturbations (e.g. failures & maintenance periods of the warehouse industrial devices, evolution of the warehouse structure, seasonality of operations, lack of resources, etc.) that an automated warehouse has to deal with, was modeled without any problem
Systemic digital twin maintenance & evolution could be regularly achieved with a very low effort
BENEFITS
Benefit #1: the very first benefit of our approach mentioned by our client was the construction of a shared global & transversal quantitative vision of an automated warehouse which was currently lacking.
Benefit #2: our approach led to the identification of optimal design choices for an automated warehouse, taking into account all the commercial & industrial constraints and hazards that it must face.
Final Assembly Line ramp-up assessment
The challenge
A commercial aircraft manufacturer is preparing to increase the production in its final assembly line (FAL) in order to meet the market demand. However, its industrial facilities are at the limit of their capacity, and one needs to understand what to do in order to achieve a successful ramp-up consisting in doubling the current production rate in the short & medium term. Our customer asked us to analyze the current weaknesses of its industrial system and to propose relevant mitigation actions in order to optimally prepare it for the targeted industrial ramp-up.
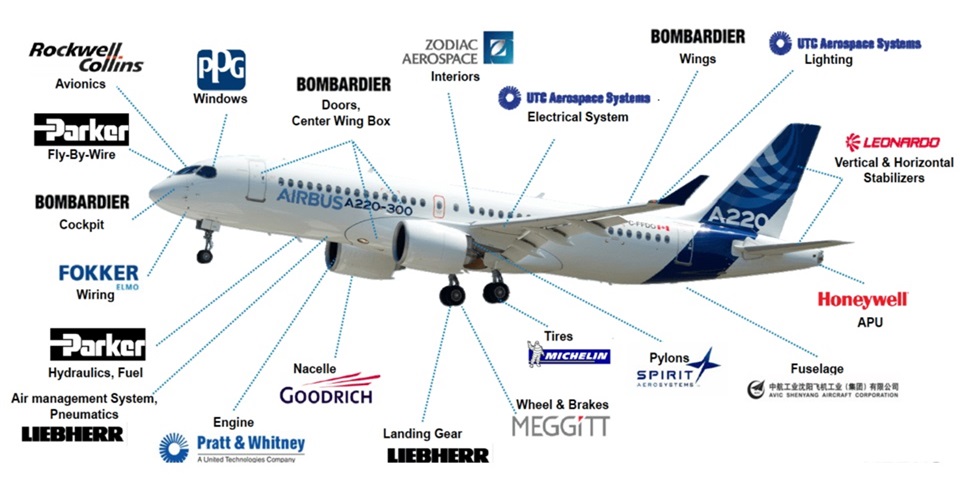
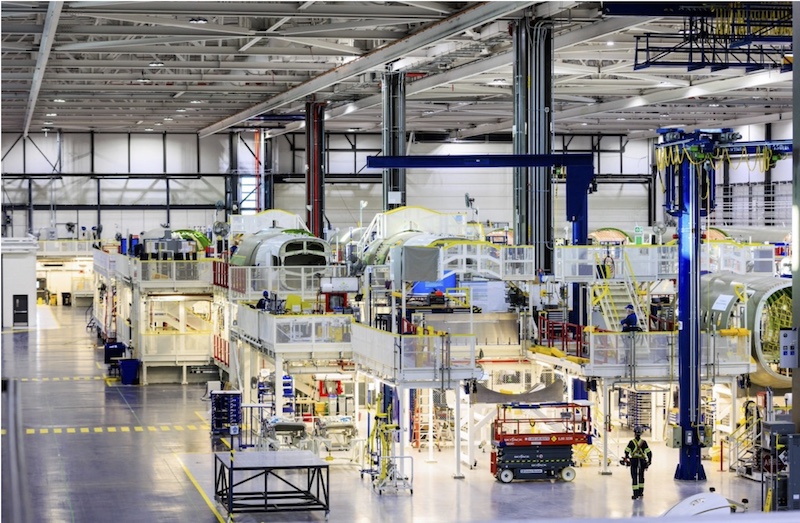
Our approach
Our response was based on the construction of a system model, supporting a corresponding systemic digital twin, for the current overall / extended industrial system, consisting in the final assembly line, the involved supply chain and the industrial governance system, together with their main internal & external stakeholders such as sales, quality, engineering, procurement, customers and regulators, relying on a realistic systemic model of this global system. This allowed us to analyze the industrial system and to evaluate its main bottlenecks in relationship to the targeted industrial ramp-up, leading to relevant and significant recommendations for industrial improvement.
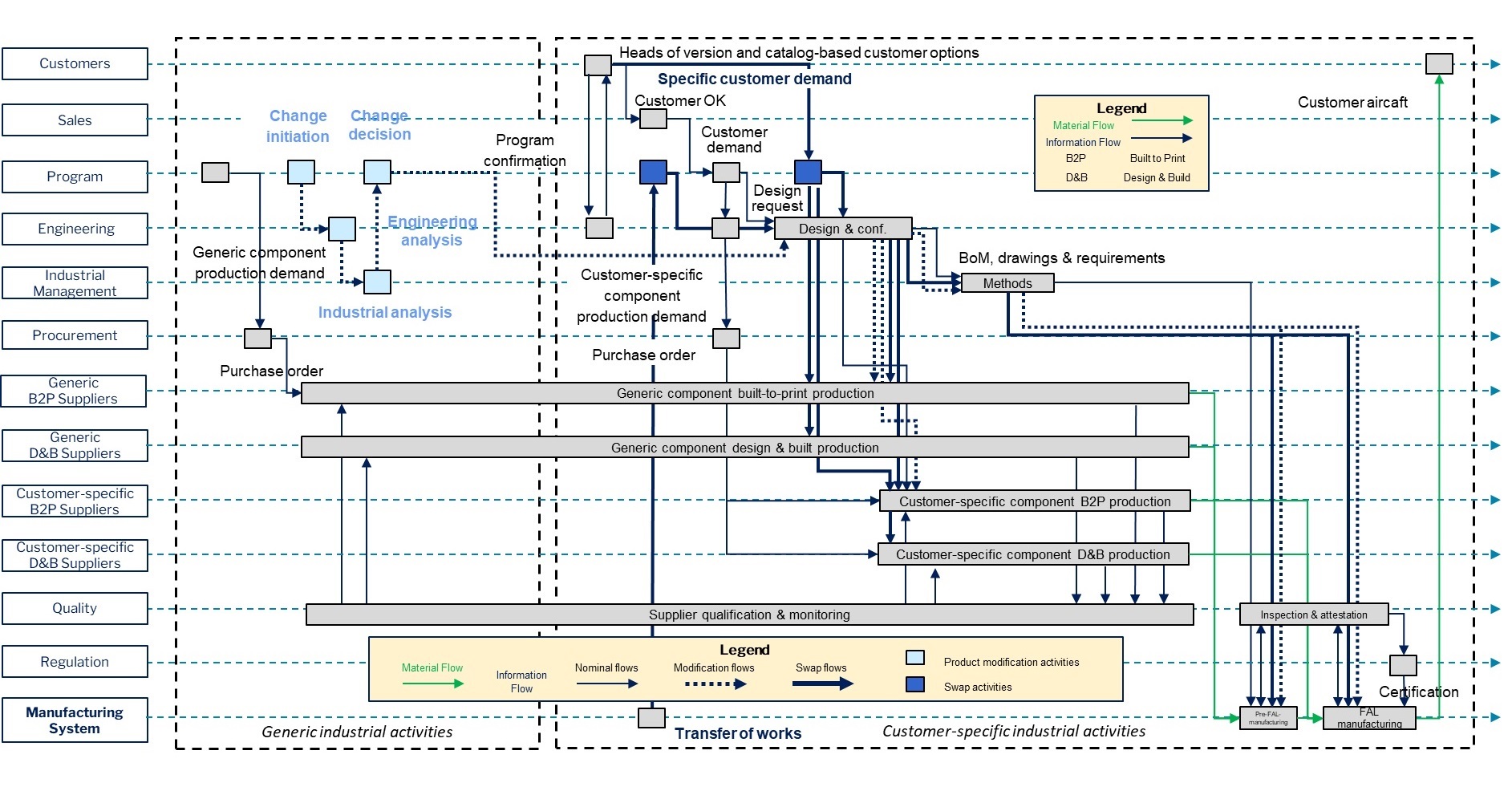
The outcomes
FEATURES
Service features that were deployed in this case:
– Structural & behavioral modeling of the overall / extended aircraft industrial system
– Analysis of operational data of the overall / extended aircraft industrial system
Product features that were used in this case:
– Development of a systemic model in Σ™
– Step-by-step and stochastic simulation
– Scenario simulation and evaluation
ADVANTAGES
Market trends were captured to model the evolution of customer demand as one of the core inputs of any aircraft industrial system.
The main business & industrial hazards & perturbations (e.g. change of design of an aircraft or evolution of customer needs during development, reranking of production, supplier issues, part shortages, etc.) that the overall aircraft industrial system has to deal withn were integrated in our system model.
Systemic digital twin maintenance & evolution could be regularly achieved with a very low effort
BENEFITS
Benefit #1: the very first benefit of our approach mentioned by our client was the construction of a shared global & transversal vision of its overall / extended industrial system which was currently lacking.
Benefit #2: our approach made it possible to identify the main bottlenecks of the existing global / extended aircraft industrial system in relation to the targeted ramp-up and to define improvement recommendations to move towards this target.